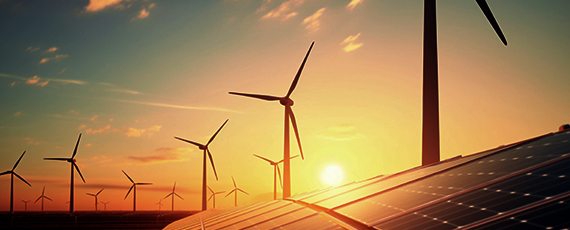
Ammonia and Energy: The Choice Between Green Innovation and Grey Tradition
Traditional ammonia, often referred to as grey ammonia, has a long-standing history. Comprising hydrogen and nitrogen, ammonia has been a foundational chemical since the early 20th century.
It is integral to the production of Nitrogen, Phosphorus, and Potassium (NPK) fertilizers, serves as a classic vapor compression refrigerant in food manufacturing, and is used in making ammonium nitrate, a key explosive in mining.
As the world shifts towards renewable resources, ammonia is increasingly recognized for its potential role in the energy transition. It serves as a hydrogen carrier, efficiently transporting hydrogen atoms from one location to another. This has led to growing interest in green ammonia, which offers a more sustainable alternative to traditional production methods.
So, what distinguishes grey ammonia from green ammonia? With federal regulations emphasizing decarbonization and sustainable development, it is essential to understand how each type aligns with a low-carbon economy. In the following sections, we will examine the production methods, as well as the associated costs and benefits of both grey and green ammonia.
Traditional (Grey) Ammonia Production
Grey ammonia is produced by combining nitrogen and hydrogen through the Haber-Bosch process. This process utilizes natural gas as the hydrogen source and air for nitrogen. Hydrogen is generated by steam reforming of natural gas, followed by a shift conversion to convert methane. This endothermic reaction uses natural gas both as a reagent and as a fuel to heat the process. The chemical equations for this reaction are as follows:

Shift Conversion:

The nitrogen is sourced from ambient air, which consists of approximately 80% nitrogen and 20% oxygen. During the reforming reaction, the air is introduced, and the oxygen combusts with natural gas to produce energy. The resulting synthesis gas is then treated to eliminate carbon dioxide, moisture, and other impurities. Carbon dioxide is ultimately released into the atmosphere.
Ammonia synthesis involves the catalytic reaction of nitrogen and hydrogen in the correct proportions to produce ammonia (NH3). This reaction is exothermic, releasing heat, as illustrated below:
Ammonia Synthesis:

The ammonia produced is then cooled and liquefied for storage in tanks. In this state, it is commonly referred to as anhydrous ammonia, characterized by its high purity of over 99% NH3. Traditional ammonia is termed “grey” due to its reliance on natural gas in the production process. If carbon capture and sequestration (CCS) technology is employed to mitigate carbon dioxide emissions, the ammonia is designated as “blue.”
Regardless of the production method or the color classification, ammonia molecules remain identical. Whether used in agriculture as fertilizer, in industry as a refrigerant, or diluted as a household cleaner, the color designation reflects the production process rather than the application of the ammonia.
Green Ammonia Production
Green ammonia production, while not entirely new, is gaining traction with the increasing focus on renewable energy sources. It is produced using green hydrogen, which is generated through electrolysis powered by renewable energy sources such as wind or solar. This method eliminates the need for natural gas, bypassing the steam reforming and shift conversion processes. Nitrogen is still sourced from the air.
In addition, advanced separation processes such as pressure swing adsorption (PSA), cryogenic air separation, or membrane technology are employed to enhance purity by removing oxygen. Green ammonia synthesis mirrors the traditional method, using nitrogen and green hydrogen in precise molar ratios.
Ammonia as an Energy Carrier
As the push for sustainability intensifies, the industry is increasingly focused on improving efficiency to reduce energy consumption. All types of ammonia—grey, blue, and green—offer significant potential as energy carriers.
One of ammonia’s key advantages is its suitability for long-distance transportation and storage. Hydrogen, while efficient in fuel cells, requires extremely low temperatures (-253°C) for liquid transport, which is energy-intensive and supported by underdeveloped infrastructure. In contrast, ammonia can be stored and transported at a more manageable temperature of -33°C. It has a higher energy density and lower cost for hydrogen transport. Additionally, ammonia can be used as a fuel, predominantly in the maritime industry. Each type of ammonia—whether grey, blue, or green—can be employed in this capacity.
Power Factors to Consider
Overall, the green ammonia process is less complex than the traditional method but demands substantial energy input, leading to higher electrical infrastructure costs. These costs vary geographically, with some of the highest expenses found in places like Hawaii and California. Typically, implementation occurs in regions with low energy costs or where nitrogen and hydrogen are byproducts of existing processes.
While grey ammonia remains cheaper to produce due to its reliance on natural gas, the transition to a carbon-free economy may warrant a cost comparison study to identify the most economically viable option.